Current systems try to keep the cables on a six-axis robot static while everything operating around them is dynamic. Instead, consider a six-axis robot as three separate sections: the sixth to third axis; the third to second axis; and the second to first axis.
The Less is More Approach to Robotic Cable Management
Contributed by | igus
Introduction
In recent years, cable management has come into the limelight because machine reliability has increased dramatically, even though robots have grown more complex. Unfortunately, the methods used to attach and guide cables have not quite followed suit. While managing cables and hoses is often an afterthought in most designs, it is truly a vital part of any well-functioning robot.
Since the 1960s, cable management methods for robots have not changed dramatically. Most experts agree that one of the top blunders made is underestimating cable management issues. For instance, during a conference hosted by the Robotic Industries Association (RIA), a group of leading system integrators cited cable issues as the number one reason for downtime in robotics cells. Headaches range from tangled and corkscrewed cables, to complete breaks that cause downtime, lost revenue and damaged reputations.1
This is why the ways in which robot cables are attached and guided is important. The less is more approach to cable management is a best practice that robotics engineers and integrators can apply. It centers on designing cable management systems for six-axis robots – including cables, hoses, tubing, carriers, and connectors – in three separate sections.
Overview of Industrial Robots
The term robot is defined as a machine capable of carrying out a complex series of motions automatically. It was first introduced in a Czech science fiction play and then in 1942, the term “robotics” was coined by Isaac Asimov, a well-known American author and professor of biochemistry at Boston University.2
By the 1970s, robotics had made its way into most manufacturing facilities, predominately in the automotive industry, and by 1980, more than 4,000 robots were being used in the US. Fast forward 30 years, and more than 1.3 million industrial robots have made their way into manufacturing plants throughout the world.3
During this robotic evolution, many different types of robots emerged. Some of the most common are:
What do all these robots have in common? The cable management system is typically left to the last minute, but without it, unprotected cables are likely to fail. Cable damage can shut down the most important robot on the line, which leads to costly downtime.
The Less is More Approach for Six-Axis Robots
Current systems try to keep the cables on a six-axis robot static while everything operating around them is dynamic. Using one, long restrictive cable package prevents movement in sync with the robot. Restrictions stress cables, which accelerates failure. Often technicians severely bind cables with excessive dress packs (protective coverings on cables), cable ties, and even duct tape. The goal is to minimize tangling and interference with the machine, but these types of solutions cause corkscrewing and failure.
Instead, consider a six-axis robot as three separate sections: the sixth to third axis; the third to second axis; and the second to first axis.
This breakdown is the key to longer-lasting cables. Each cable section needs a minimal dress pack, strain relief with service loops, and a junction box that contains and protects the electrical connectors joining the cables.
Use of a strain relief mechanism can eliminate stresses and extend the service life of a moving cable. This strain relief may consist of standard elements such as tie wrap plates or clamps. Engineers should ensure the cables are in the neutral axis, not touching the inner or outer radius of the cable management system.
Download and read the complete White Paper here
The content & opinions in this article are the author’s and do not necessarily represent the views of RoboticsTomorrow
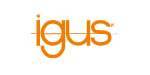
igus
The mission of igus® is to use its innovative polymer materials to develop products that provide creative solutions and exceed our customers' expectations while delivering fast, accurate service.
Other Articles
Low-Cost Robotics Elevate Industrial Inspection Processes
7 Cable Management Mistakes to Avoid
New Exoskeleton is Revolutionizing Work Processes
More about igus
Comments (0)
This post does not have any comments. Be the first to leave a comment below.
Featured Product
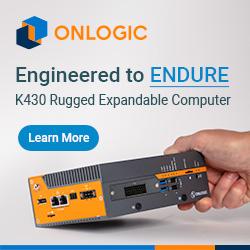