Weve put together a breakdown of the cost of automation, and how to justify it to the leadership team.
Rita Brunk | Genfour
While robotic process automation offers businesses a whole host of benefits, some organizations are struggling to get the idea past the decision making committee. Cost is, of course, a huge determining factor as to whether an organization chooses to go ahead with a project. We’ve put together a breakdown of the cost of automation, and how to justify it to the leadership team.
Related hardware costs based upon the hosting location
Robotic process automation software is best suited to automating processes that are found within core operations. Often, requirements are too tactical or immediate to justify complicated and lengthy IT development. Opting for robotics enables organizations to automate processes quickly and cost effectively. While an onshore full-time equivalent (FTE) costing $50K can be replaced by an offshore FTE for $20K, automation software can perform the same function for $5K or less – without the drawbacks of managing and training offshore labor.
Typically, between 70-80% of rules-based processes can be automated, which means that companies can operate onshore, at a lower cost point than offshore. Keeping business operations onshore means that there is no need to rely on an offshore or outsource partner, so you can maintain absolute control of the throughput. Many companies whom have chosen the outsourcer route are now finding themselves with a lack of understanding of their own processes. In other words, they need to query their outsourcer on how something is done.
Development costs
Automation via robot, can be implemented in a number of weeks, and achieves a return on investment quickly, with an average payback time of three to nine months. It doesn’t replace any existing systems and is non-invasive, thus there is no need for existing systems to be re-engineered. In fact, it is even possible to reconsider some ERP projects previously deemed unacceptable due to long payback, by instead developing a robot. Some automation providers offer customers the option to pay as you go, so you can pay once the automation software is in production, delivering you benefit. Many accounting policies will also allow you to capitalize the cost over two to three years.
Ongoing costs and licensing
Most robotics software providers will look to sell you a license, or an enterprise license, which for large companies can cost upwards of $1M. A more cost effective option is to trial a number of robotics services companies to see which software is the best fit for your business.
Unlike other cloud based ERP/ applications, there are no ongoing professional services other than maintaining the license that are required. You may choose to have a minimal amount of training for your team in the beginning so that development of subsequent robots goes smoother. In addition, unless you plan to build your own robotics staff, you may choose to have the service provider maintain your robot at a fairly reasonable cost.
Cost savings and cost avoidance
You will need to take into account the costs you incur for full time/temporary onshore/off shore employees to handle fluctuating volumes of business throughout the year. Training up a team requires time and resource. You will also need to consider the predictability of robotic process automation – an automated process is available around the clock, and is able to scale up or down quickly, according to demand. On average, a robot can handle the volume of three full time employees.
The ability to ramp up a process quickly to manage demand due to business growth or cyclical volume peaks is easily achievable when robotic process automation is implemented to cover selected core processes. This enables companies to meet peaks in demand by dedicating more resource to any process, without recruitment, training requirements or overtime costs.
Robots never give their notice. Calculating recruitment cost savings is a quick and easy way to demonstrate the benefit of robotic process automation to the leadership team. Recruitment may be a specific pain point for one of your decision makers, so be sure to prioritize it early on in your business case.
Look out for our sixth blog in the ABC of RPA series, where we will be discussing how robotics and automation works alongside IT departments.
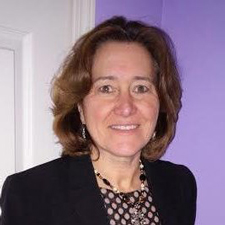
Rita Brunk is the Robotics and Automation Transformation Lead for the US at Genfour, the robotic process automation (RPA) and AI delivery specialist. Rita has seven years of automation experience within a shared services environment, which developed to incorporate robotics tools.
Prior to joining Genfour, Rita led a global shared services effort at Hewlett Packard for robotics. She opened and closed various captive shared services sites outside of the US, and several sites under her responsibility won SSON Excellence Awards for value creation in a mature shared series centre.
For the past 15 years, Rita has held a number of executive positions in a captive shared services environment focused on process optimisation and the development of analytics within the finance, HR, logistics, procurement and marketing functions. During this time, Rita oversaw large teams located in Michigan, India, Costa Rica, Argentina and Mexico. For the last two years, she led global efforts to reduce headcounts across all locations, implementing RPA to drive this progress.
The content & opinions in this article are the author’s and do not necessarily represent the views of RoboticsTomorrow
Comments (0)
This post does not have any comments. Be the first to leave a comment below.
Featured Product
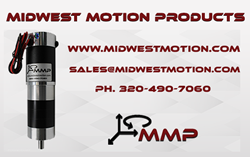