Luckily, robotics can adapt to changing sizes, using end-of-arm tools that can adjust their grips on the items that need to be handled.
Contributed by | Axium
There has always been a trip from factory floor to store shelf for CPG (consumer packaged goods), but now that trip is fraught with logistical challenges. We can thank many of the current difficulties in shipping on the changes taking place at retail outlets, as well as with packaging needs, personal preferences and environmental considerations.
Big-box stores such as Costco have increased sizes of packaged goods and numbers of items packaged together, while other stores have introduced the way products are mixed and matched such as variety packs and single-serve items. That means more SKUs (stock-keeping units) and more complexities for the distribution centres that line up the items to be shipped out. More SKUs translate into increased production lines.
Stores like Costco and Walmart also dictate guidelines on size, requiring manufacturers to display items according to company standards. Many of the boxes need to be store ready and be set up with as little handling as possible.
That results in fewer of those traditional corrugated boxes. They would normally be used to ship out neat stacks of goods that are then unpacked by store clerks. But now manufacturers are packaging many products in ways that can have them instantly converted into display cases. That type of container will often have a perforated top easily torn off so that shoppers can then pull out an item from the box that bears both the product’s logo and appealing graphics.
This hodgepodge of dimensions again translates into more production lines due to each display case’s unique handling requirements. Luckily, robotics can adapt to changing sizes, using end-of-arm tools that can adjust their grips on the items that need to be handled.
Some other packaging innovations and environmental changes, however, bring about bigger challenge to the automation process.
Take items like thinner water bottles. In the past the thicker plastic could be gripped by a robot using suction. Now, grip one of those bottles harder than you would shake someone’s hand and you end of hearing that loud cracking sound that in a distribution centre can mean broken-open bottles. Robotic grippers are becoming more sensitive so as to adapt to these changes, while new palletizing techniques that handle items from more points take the fragility of new products into consideration.
Due less to environmental considerations but resulting from a packaging innovation, many bottles and other items are now encased for consumers not in right-angled boxes but are form-fitted into thick clear plastic. Again, the unique dimension takes away from the standards that would have made for more easy-to-grip and easy-to-stack items.
All these changes in consumer packaged goods have given robotics companies new challenges, but ones that have not been insurmountable.
One example of improved handling of consumer packaged goods has been a change in the forklift mentality. Robotics can simply increase the number of forks below a package so that the weight of the more fragile and less standard-sized item can be better distributed. It can then be easily picked and moved down the production and through to the palletizing process, and then swiftly onto that traditional trip to the store shelf. With the combination of proper tooling and robotics, flexible case packing and palletizing, and mixed load palletizing, are now proven alternatives that can be efficiently used by CPG manufacturers to fulfill their new challenges.
The content & opinions in this article are the author’s and do not necessarily represent the views of RoboticsTomorrow
Comments (0)
This post does not have any comments. Be the first to leave a comment below.
Featured Product
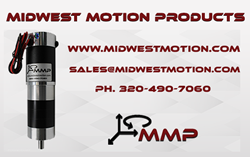