Prosthetic technology is advancing rapidly, but not without sticking points.
Len Calderone for | RoboticsTomorrow
In 1974, a television series starring Lee Majors as NASA astronaut Steve Austin premiered. Austin is severely injured in the crash of an experimental aircraft. He is "rebuilt" in an operation that cost six million dollars. His right arm, both legs and the left eye are replaced with "bionic" implants that enhanced his strength, speed and vision far above human norms. He was able to run at speeds of 60 mph and his eye has a 20:1 zoom lens with infrared capabilities, while his bionic limbs all had super-human powers.
Cybernetics is now catching up to science fiction. If you remember Star Trek's Data, his arm is often opened for repairs similar to the picture below. Or, how about The Twilight Zone segment, "I Sing the Body Electric," in which a family selects different body parts to create a nanny. All the parts are put together and a robotic nanny comes out.
Today, we are rebuilding damaged bodies with prosthetics similar to the bionic parts given to Steve Austin. There are more than 2 million amputees in the US alone. Scientists are working on prosthetics that reflect the properties of a biological limb. They must have sensors for touch, temperature, vibration and the ability to sense the limb's position relative to other body parts. They also need to have extended use with mechanical components that will provide strength and tolerance to heat, cold, water, humidity, dust, etc.
Urethane is the perfect material for the high demand environments of prosthetic limbs. It can be constructed soft as a sponge, or hard as steel and it has extensive wear and elasticity characteristics. Urethane parts provide longer service life when compared to plastics and rubber, along with lower noise abatement properties when compared to metals.
The prosthetics company, RSLSteeper, has developed a robotic arm that can operate by twitching the muscles in the upper forearm. The arm has been programmed with 14 different grips that approximate human behavior, from a one-fingered point to a flexed fist that allows a person to carry heavy objects. A test subject can tie his shoes and click a computer mouse. The bio-limb even comes with a synthetic skin that matches a person's own skin tone. The device—known as the bebionic3 myoelectric hand—costs about $40,000 to outfit a patient with it.
A British man who lost his arm in a horrific smelting accident has been fitted with a bionic arm so precise that he can now type and crack raw eggs.
New materials and imaging technology have made these devices stronger and lighter with miniaturization leading to small efficient motors and solenoids that can operate the fingers individually. The prosthetic hand was transformed into a powerful tool for people with hand amputations. The robotic hand uses muscles of the upper arm to move its fingers. As a muscle contracts, the electrodes attached to the skin send an electrical signal to actuators and movement is produced.
Leg prosthetics have come a long way, from the foot blades to exoskeletons. They now come with their own motors that run the pistons that stand in for muscles. These devices have sensors that can detect the angle of the prosthetic knee and the pressure on the artificial foot. They can detect how fast the prosthetic is moving. All of this information is fed into a controller that acts as a central nervous system for the limb, coordinating all the information so the limb moves smoothly.
The prosthetic has powered knee and ankle joints that operate in unison. It comes equipped with sensors that monitor the user’s motion. It has microprocessors programmed to use this data to predict what the person is trying to do and operate the device in ways that facilitate these movements.
There is a control algorithm that determines the leg’s position and motion using sensors; and then performs a single calculation to determine when force should be applied. This makes it computationally and energy efficient, and also provides for a very natural gait, as tests by amputee volunteers show.
Going up and down slopes is very hard with a conventional non-powered leg, tiring out the patient. But with a powered leg, that becomes a non-issue because it goes up and down slopes almost like a natural leg. Another problem is stumbling. Engineers have now added an anti-stumble routine. If the leg senses that its user is starting to stumble, it will lift up the leg to clear any obstruction and plant the foot on the floor.
Engineers have been able to produce a prosthetic leg that weighs about nine pounds – less than most human lower legs – and it can operate for three days of normal activity, or 8 to 10 miles of continuous walking on a single charge.
Rehabilitative prosthetics have been built around rigid exoskeletons. They support a patient’s limb but are short on flexibility. In newer designs, flexibility is achieved by going beyond the rigid exoskeleton. The new designs employ a series of long, tubular pneumatic artificial muscles, lightweight flexible sensors and advanced control software to regain the most important properties of a ridged exoskeleton.
When connected to the human body, the flexible robotic prosthetic uses a foot bed to anchor the system. With a human limb in place, the foot bed is connected to the thigh by means of long tubular pneumatic artificial muscles that run up the side and back of a patient’s leg. To control the constriction of the pneumatic artificial muscles, “hyper-elastic strain sensors” generate and send signals to the prosthetics control system as they flex and contort into new shapes. With very quick reaction, the new prosthetic can actuate a patient’s limb immediately, simulating natural movement.
The Alpha IMS retinal prosthesis, developed by the University of Tübingen in Germany, is an implanted bionic eye. It is connected to a patient's brain via 1,500 electrodes, providing unparalleled visual acuity and resolution, as well as being completely self-contained. The Alpha IMS prosthesis has a built-in sensor that directly gathers its imagery from the light that passes into the patient's eye. This allows the patient to swivel their eyeballs normally. In essence, Alpha IMS is the first true, self-contained bionic eye.
Every few months, there’s exciting news about the latest in prosthetic technology.
Prosthetic technology is advancing rapidly, but not without sticking points. For most people, these state-of-the-art devices are neither attainable, nor are they a fit for day-to-day life. For the average patient, something far simpler is often better. One in every 190 Americans currently lives with a lost limb with about 80% of these due to vascular diseases such as diabetes. Because of weight gain, cardiovascular issues and general immobility, it is difficult for amputees with vascular diseases to get up and walk again after an amputation, never-the-less use a prosthetic.
Even those, who are fit, mobile, and looking to get the most advanced technology, face the problem of cost. Prosthetic technology has advanced, but while research continues, amputees are faced with choices about how to maximize their mobility in a way that fits their needs and lifestyle.
For more information:
- http://techdigest.jhuapl.edu/TD/td3003/30_3-Johannes.pdf
- http://techdigest.jhuapl.edu/TD/td3003/30_3-Biermann.pdf
- http://techdigest.jhuapl.edu/TD/td3003/30_3-Moran.pdf
- http://techdigest.jhuapl.edu/TD/td3003/30_3-Armiger.pdf
Len Calderone - Contributing EditorLen contributes to this publication on a regular basis. Past articles can be found with an Article Search and his profile on our Associates Page He also writes short stores that always have a surprise ending. These can be found at http://www.smashwords.com/profile/view/Megalen.
|
![]() |
The content & opinions in this article are the author’s and do not necessarily represent the views of RoboticsTomorrow
Comments (0)
This post does not have any comments. Be the first to leave a comment below.
Featured Product
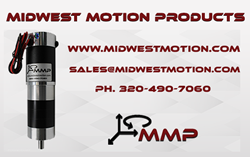