In most industrial settings, robots speak one language and the plants within which they work speak another.
Breaking down the robot-factory language barrier
Chetan Kapoor | Yakawa
In most industrial settings, robots speak one language and the plants within which they work speak another. Mr. Kapoor and his colleagues think this makes communicating with and manipulating robots unnecessarily difficult. An engineer or technician must know the factory's programmable logic controller (PLC), which is the factory's language, and learn a robot language to put a robot to work.
Why do robot designers require factories to learn another programming language when integrating these machines into industrial applications?
Industrial robots were invented and deployed before programmable logic controllers (PLCs). As such, they have evolved with a programming language that is suited to robotic application programming. This language is also a form of product differentiation for robot companies and well accepted by traditional robot users such as the automotive industry.
How much time and energy does it take factory personnel to communicate with their robots?
If the solution is being developed by PLC programmers, they can spend considerable time trying to learn how to make a robot communicate with a PLC as well as learning to program the robot in its own proprietary language. This problem is often addressed by having two programmers: one for the PLC and one for the robot. Together, they can be efficient, but the integration is fairly low level and the amount of information exchanged is limited.
What sparked the idea at Yaskawa of making its robots use the factory PLC?
Yaskawa’s decision to do this was driven by three market trends:
- Almost all robot applications have a PLC that handles overall cell control;
- There are a limited number of available robot programmers compared to the talent that understands PLCs;
- There is an increasing sophistication of PLC software and computational power.
Can the language barrier be solved with legacy robots operating at plants, or does the fix require purchasing an entirely new machine?
It is possible to do retrofits on some legacy robots. However, these retrofits only make sense when a company can retrofit a large quantity of the same robot model. In most instances, it would be more cost-effective to get a new robot with PLC controls and programming.
How does it work and what is the process to make the language conversion?
PLC programming languages and HMI software have evolved to a point where they now support the creation of custom instructions and powerful application specific HMIs. We have used these capabilities to create robot instructions that look and feel similar to PLC instructions as well as an HMI to configure, teach, and maintain the robots. Using these instructions and HMI, a PLC programmer can program the robot entirely through the PLC software without learning any new programming languages.
What were the challenges to developing robots that could understand the factory's language?
Both marketing and technical challenges exist. On the marketing side, the challenge is educating the customer against the status quo and clearly communicating the applications that will benefit from PLC programmed robots. On the technical side, the challenges are related to implementing the robot application software modules (e.g., palletizing, picking, painting, etc.) on the PLC platform.
Do you see a day when the factory and its robots will all speak the same standardized common language?
We do not expect a common robot programming language that all robot makers will agree on. On the PLC side, the IEC 61131 programming language standard already exists, and we expect this to have more of an impact in standardizing the programming of robots. The success of this will depend on the success of PLC controlled robots in general.
Are there any other developments at Yaskawa that we should know about?
Yaskawa is the only major maker of robots and motion products. We are the world leader in making products for anything “that moves intelligently” in factories. Over the next few years, you will see increasing unification between our motion and robot products and this unification will be largely driven by common PLC programming software for both motion and robots.
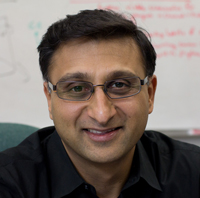
associate director and chief scientist for the University of Texas at Austin from where he received his doctorate degree in mechanical engineering.
The content & opinions in this article are the author’s and do not necessarily represent the views of RoboticsTomorrow
Comments (0)
This post does not have any comments. Be the first to leave a comment below.
Featured Product
