The gripper spider for fiber composite components is a great example how significant this contribution to the intelligent factory can be in practice.
Industry 4.0 Ready: Vacuum Solutions for the Intelligent Factory
Contributed by | Schmalz
Schmalz launched a vacuum generator with IO-Link interface back in 2008 – long before the subject of Industry 4.0 became known to a wide professional public. Today, the vacuum specialist markets numerous vacuum solutions. These make production processes more efficient, productive and flexible whilst making a vital contribution to the intelligent factory. The company is also the first manufacturer to combine sensor and actuator functions with 4.0-compatible devices.
The gripper spider for fiber composite components is a great example how significant this contribution to the intelligent factory can be in practice. In this application the spider is equipped with 15 needle grippers. A production changeover takes around 12 minutes when using conventional needle grippers. This time includes tests that are required after the changeover and processes, such as stopping the machine and reparameterizing the components. If the grippers are changed once a day, the approximated costs for downtime are around $670 for each working day ($56/minute). If the spider is running 300 days each year, this results in approximated annual downtime costs of $201,000 when using conventional grippers. With the intelligent needle gripper SNGi-AE from Schmalz, set-up times and downtime for this spider can be almost completely eliminated using remote parameterization via IO-Link.
The example describes an important feature of Industry 4.0: A modern production system is made more flexible, more productive and more efficient by using an intelligent component. A further feature enabled by the needle gripper SNGi-AE is greater manageability of the increasing complexity of products: Using fixed definable process profiles, the gripper's needle stroke can be adjusted freely. The profiles can subsequently be called up in any order for each individual cycle. At the same time, the gripper communicates with the higher-level controller and provides complete condition data. This not only allows continuous stroke monitoring but also comprehensive process control, which in turn enables ongoing process optimization.
Reducing Downtimes in the Automatic Sheet Metal Handling
Application
Tooling in a press line for the production of car body parts in the automotive industry
Handling Task
- Transfer of components between the individual presses
- Automated handling with minimum cycle times
Schmalz Solution
- Compact ejector X-Pump SXMPi-PC with intelligent energy and process control
- High suction volume of up to 220 l/min
- Power blow off module for minimum cycle times
- Monitoring, analysis and interpretation of all critical process parameters
- Energy monitoring for the optimization of energy consumption
- Condition monitoring for increasing system availability
- Predictive maintenance function
- IO-Link interface for bidirectional communication with higher-level field bus systems
Schmalz compact ejector X-Pump
Customer Benefits
- Increase in production rate by minimizing downtimes
- Simple and fast system optimization
- Identification and prevention of incorrect tooling configuration
- Significant reduction of energy consumption
- Optimization of process parameters during operation
- Early error detection before the system is shut down
- Error correction in the planned maintenance (predictive maintenance)
Savings Potential Using the Example of a Press Line in the Automotive Industry
The compact ejectors X-Pump of Schmalz increase system availability for automated sheet metal parts handling. They constantly monitor the condition of the tooling, detect subtle changes or impending failures and report them to the system controller. The user can establish a planned, preventive maintenance before the system is down. Solely by reducing downtime by one minute per day in the example an annual saving of up to EUR 300,000 can be achieved. The actual savings will vary depending on the failure cost of the plant.
Flexible Production of Fiber Composite Components without Set-up Times
Schmalz needle gripper SNGi-AE
Application
Production line for composite components with a gripper spider of 15 needle grippers
Handling Task
- Reliable, automated handling of composite textiles
- One product changeovers per day
- Each product requires different needle strokes due to different material thicknesses
Schmalz Solution
- Needle gripper SNGi-AE for handling non-rigid and highly porous materials (primary textiles)
- 10 crossed needles offering high holding forces
- Needle stroke (max. 3 mm, 10 mm or 20 mm) is freely adjustable using definable process profiles
- Stroke can be adapted for each cycle in any order
- Handling of individual layers and stacks with a single gripper
- Continuous process monitoring (stroke and energy consumption)
- IO-Link interface for bidirectional communication with higher-level field-bus systems
Freely adjustable needle stroke
Customer Benefits
- Elimination of setup and downtime during production changeovers
- No manual setting and control directly at the gripper and no test runs required
- Minimal risk of incorrect settings
- Increased flexibility of production lines (small batches)
- Error detection during operation and error correction in the planned maintenance (predictive maintenance)
- Automatic reparameterization in the case of exchange of separate grippers
Saving Potential Using the Example of a Gripper Spider for Composite Components
The spider in this example is equipped with 15 needle grippers, a production changeover takes around 12 minutes when using conventional needle grippers. This time includes processes, such as stopping the machine, reparameterizing the components and also tests that are required after the changeover. If the grippers are changed once a day, the approximated costs for downtime are around $670 for each working day ($56/minute). If the spider is running 300 days each year, this results in approximated annual downtime costs of $201,000 when using conventional grippers. With the needle gripper SNGi-AE from Schmalz, set-up times and downtime for this spider can be almost completely eliminated using remote parameterization via IO-Link.
The content & opinions in this article are the author’s and do not necessarily represent the views of RoboticsTomorrow
Comments (0)
This post does not have any comments. Be the first to leave a comment below.
Featured Product
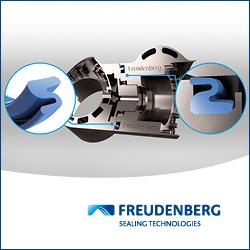