SMACs LAR Series linear-rotary actuators provide the ideal technology for improving capping quality while cost-effectively providing 100% real time on- and off-torquing validation.
Contributed by | SMAC
WHO
A major filling company approached SMAC to help them develop a new, cost-effective way for capping containers at high speeds. They wanted to achieve tighter, 100% validatable tolerances for on-torque as well as validate off-torque. The solution would need to be highly flexible to accommodate the large variety of caps and containers run on the line. Improving speed, productivity and quality were also high priorities.
CURRENT TECHNOLOGY
Most high speed capping is done on continuous motion equipment using a capping chuck with a clutch mounted on a vertical shaft. As the chuck moves around the dial, it is spun as it comes in contact with a stationary friction band or surface. The chuck spins the cap onto the container as it travels down the vertical shaft. Once the approximate on-torque is reached, the clutch disengages the chuck from spinning.
The height of the final cap placement is commonly checked downstream of the capping equipment where one sensor checks for the presence of the cap and another sensor checks that the height of the cap does not exceed a certain height. A cap that is too high can indicate that the cap was not screwed on all the way or cross-threaded. This design usually requires 4 sensors, a PLC and a stand-alone reject device. Alternatively, the inspection can be done with sensors on the capping dial but this can be complicated and more expensive.
The challenge with properly on-torquing a cap and validating the offtorque to remove it has been compounded by recent trends to reduce bottle packaging costs. This is often done, in part, by reducing the height/ profile of the cap. The difficulty of the consumer removing lower profile caps and the associated customer dissatisfaction was a barrier for limiting the height of a cap until recent economic pressures forced manufacturers to push through this barrier. Couple a low profile cap with an excessive off-torque to remove it and the manufacturer could have a perfect storm of customer dissatisfaction.
PROBLEM
Using a clutch and chuck is bulky, and involves a lot of components and processes. This method has appreciable variances in on-toque forces and no off-torque validation. Using clutches makes it difficult to detect cross-threaded caps and often requires additional downstream inspection and reject equipment. The design necessitates manual adjustments and/or change parts to accommodate different size containers, which equates to additional downtime and lost productivity. For some filling companies this method is “good enough.” Not for SMAC.
SOLUTION
SMAC’s LAR Series linear-rotary actuators with a history in the field of 15+ years, provide the ideal technology for improving capping quality while cost-effectively providing 100% real time on- and off-torquing validation. Built-in force, torque, speed and stroke control and feedback can be used to optimize the process without need for additional external sensors and checking stations. They also provide the flexibility to perform push-button changeover for different height containers. Unlike a servo motor, each SMAC actuator contains both a linear axis and rotary axis all in one unit that is controlled by one, easy to set up controller. All at a life-cycle cost less than the current approach.
“We started out just trying to help a customer build a better mousetrap,” remembers Mike Ferris, SMAC’s Western Regional Sales Manager. “Once we got into all the pain points associated with the current capping equipment we realized how much value there was in SMAC’s innovative approach.”
Improved On-Torque Process
Each station on the dial is equipped with an SMAC linear-rotary actuator. The cap is then lowered by the linear axis onto the container threads. As the cap is spun onto the container using the rotary motion, the actuator continuously monitors both the torque and stroke to validate that they both match the thread profile. Once the actuator detects a spike in torque associated with seating the cap or cross threading, the rotational motion is stopped.
Additional Off-Torque Measurement
Once the cap is torqued on, a minutely small reverse off-torque can be applied and measured for every cap. This reverse torque can be small enough to prevent damage to the tamper evident band. The cap is then rotated back to the exact position before the off-torque was measured.
Built-In Validation
Because of the built-in force, torque, speed and stroke feedback on each actuator, the presence of a cap and proper on- and off-torquing are all performed and validated using the same SMAC actuator. All this is validated on the dial so no additional downstream inspection stations are needed.
Performing Difficult Capping Process
Because of the complete control of both the rotational and vertical axis, difficult to thread caps can be easily handled. The actuator first counter-rotates the cap until the drop in force associated with the start of the threads is detected. Then the cap is rotated forward.
Increased Durability and Reliability
SMAC actuators have an initial life expectancy of >100 Million cycles. Direct electric drive means no clutches, bands and bearings to maintain, replace or adjust.
Increase Flexibility
Programmable rotational and liner motions means almost limitless changeover can be quickly and accurately done with the push of a button. This electronic changeover results in reduced scrap and downtime which equates to much higher line efficiencies.
Reduce Equipment Footprint
Faster, more accurate capping process means fewer stations are needed on the dial and/or faster throughput can be achieved with the same size dial. The overall footprint can be reduced because no separate downstream inspection device is needed.
About SMAC Moving Coil Actuators
SMAC has been making true mechatronic actuators since 1995. Programmable variable control of positions, speed, and force are combined with the ability to do work and verify its success. SMAC Moving Coil Actuators are the finest mechatronic actuator designed and built for the 21st century.
We are committed to delivering optimal solutions at competitive prices for industrial motion applications.
SMAC manufactures a wide range of precision programmable electric actuators based on its patented moving coil technology. These proprietary and patented moving coil linear motor based designs are technically far ahead of old generation pneumatic and other electric actuators, including moving magnet linear motors. Our technological edge, combined with continuous cost-down/quality-up process and its worldwide sales basis makes SMAC the most dynamic electric actuator manufacturer in the world today.
The content & opinions in this article are the author’s and do not necessarily represent the views of RoboticsTomorrow
Comments (0)
This post does not have any comments. Be the first to leave a comment below.
Featured Product
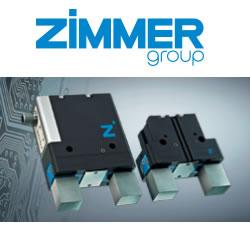