Here you will find a summary of some of the great new products and innovations from Automate 2015:
RoboticsTomorrow Team
Automate showcases the full spectrum of automation technologies and solutions. From traditional industrial applications to cutting edge new technologies, you'll find ways to automate every process in your company. It's held just once every two years and this year RoboticsTomorrow.com is once again a media partner for Automate 2015 and we have expanded to bring more news, articles, products and perspectives from the show.
Here you will find a summary of some of the great new products and innovations from Automate 2015:
igus - The Triflex RSP system 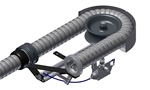
The Triflex RSP system is designed for cable guidance on robots performing complex movements. The adjustable pneumatic retraction system safely guides the cable package, and can be attached to various robotic models quickly and easily. Lightweight and space-saving, Triflex RSP is also available with optional monitoring system for robots whose program sequences frequently change, alternate, or are not 100-percent predictable.
Festo - The MS Series Quick Order Guide
The MS Series Quick Order Guide is intended to help you select products which are stocked or assembled in the North American production facility, providing you with the best possible lead times. All of the configuration options in this document are assembled in the North American production facility. All of the material numbers of the most common individual components in this document are stocked in the North American production facility.
Schunk - EGN and EZN Safety Gripping Systems 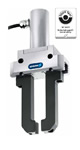
The robot is in normal operation. The operator announces his or her entrance in the robot safety zone by pressing a button at the door. The door unlocks, and the operator enters the safety zone while the robot and the gripper slow down to the safely limited speed (SLS) at the same time. The operator enters the second safety zone to take the workpiece. The robot and the gripper switch into the safe operating stop while remaining continuously powered (SOS). If a workpiece is held by the gripper, it remains safely held.
If the workpiece has not been laid down by the robot with the gripper, the operator steps back into the first safety zone: In order to lay down the workpiece correspondingly, the robot and the gripper automatically continue moving at the safely limited speed (SLS). After the storage process, the operator enters the second safety zone again to take over the workpiece. The robot and the gripper switch into the safe operating stop (SOS). When the operator leaves the safety zones and closes the door, the robot and the gripper operate normally again.
IPR Robotics - Right-Sized 7th Axis Robot Linear Rails
IPR Robotics offers a wide range of servo-driven 7th axis linear rails for industrial robots. These rails come in ten different sizes and are constructed from modular high strength extruded aluminum sections to handle payloads of 100 kg to 1600 kg or from steel to handle 2000 kg payloads. This variety of rail sizes allows each application to be sized correctly, controlling the space required and the price point. The drive train design of these rails utilizes helical gear-racks and is proven over 10 years to be repeatable and reliable, even in tough foundry applications.
maxon precision motors, inc. - MAXPOS 50/5 Positioning Controller 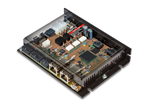
Epson Robots - LS SERIES SCARA ROBOT
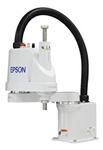
Staubli - New Safety Functionalities 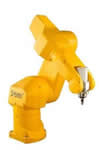
ATI Industrial Automation - Lateral and Pivoting Compliance Devices
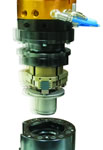
MICROMO - FAULHABER 3274…BP4 Brushless DC Motor
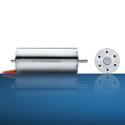
DE-STA-CO - 100 Years of Innovation 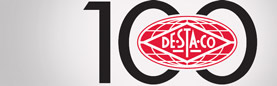
DE-STA-CO will kick off its 100th anniversary celebration at Automate next week by looking back on the company's history, while also introducing innovative new products for OEMs and end-users.
MICROMO - FAULHABER 3890…CR DC Motor 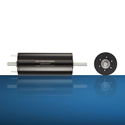
MICROMO is pleased to announce the latest addition to the FAULHABER CR DC Motor series. Its graphite commutation, powerful neodymium magnet and particularly high copper content in the FAULHABER rotor winding provide the compact 3890 CR with an enormous amount of power.
Universal Robots - UR 3
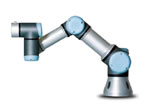
Jabez Technologies - RobotMaster .jpg)
Intelligrated - Robotic mobilization solution for RTS™ GoKart
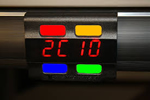
Adept Technology - New Fleet Management System for Lynx Mobile Robots 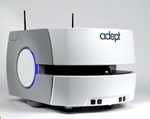
Nachi Robotics - The new MZ Series robot arms
The new MZ Series robot arms feature ultra high-speed motion capability with advanced through-arm dress capabilities to simplify routing of hoses and cables for material handling, assembly, vision and many other applications. Boasting an IP67 rating, MZ Series robots are the fastest in class in standardized speed testing, leading all competitors' robots. Flexible mounting solutions allow MZ Series to be floor, wall, or invert mounted to better suit customers' needs for any given application. As the newest addition to Nachi's comprehensive robot lineup, MZ Series robots build on the great heritage of large payload robots by providing an extremely versatile small robot with top of the line capabilities. The MZ03EL incorporates the same great features as other MZ Series robot with added reach up to 1.1 meter horizontal reach for larger work areas.
ABB Robotics - IRB 1200 Robot with the ABB FlexFeeder
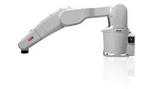
OCTOPUZ - Robotic programming software 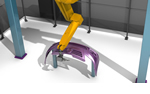
OCTOPUZ is an intelligent CAD-to-Path and offline robot programming and simulation software solution ideal for any path-sensitive application. Created in 2013 by In-House Solutions, the company took a revolutionary approach by combining the offline programming of robots with a manufacturing process simulation. Today, OCTOPUZ provides a mainstream, versatile, powerful and effective solution for any robotic challenge.
"OCTOPUZ allows us to show the industry how we can provide the best in automation solutions using simulation-based software," said Greg Culp, Robotics Sales Manager at In-House Solutions. "It gives us the ability to visually describe and 3D animate proposed solutions tailored to the customer's specific automation needs."
GÜDEL - LINE OF ROBOT TRACKS AND GANTRIES
For the first time, Güdel previews a vertical TrackMotion at a major industry exhibition. Furthermore, attendees are treated to demonstrations of Güdel's third generation technology for gantries and tracks.
Harmonic Drive LLC - HPN Harmonic Planetary® Gearhead 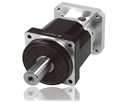
Harmonic Drive LLC will be showcasing its breadth of zero-backlash and low-backlash products at booth 1035. New on display will be our HPN value-line of Harmonic Planetary® gears. HPN Planetary Gears offer affordable pricing with short lead times. HPN Planetary gearheads feature a robust design utilizing helical gears for quiet performance and long life. These gearheads are available with short lead times and are designed to couple to any servo motor with our Quick-Connect coupling. This new value series of planetary gears carry the reputation for quality and reliability for which Harmonic Drive® products are known throughout the world. HPN gearheads are suitable for use in a wide range of applications for precision motion control and positioning. HPN Harmonic Planetary® gears are available in 5 frame sizes: 11, 14, 20, 32, and 40, with reduction ratios ranging from 3:1 to 31:1.
Tolomatic - RSA-HT electric rod-style actuators deliver up to 12,900 lbf

Harry Major Machine (HMM) - Cable-less Gantry System 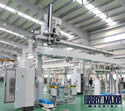
Here is a look at some of our other coverage:
Our Special Automate Newspage is full of News and Press releases from the show.
Our Automate Product Page showcases some great products and Automate booth numbers for our supporting advertisers.
The content & opinions in this article are the author’s and do not necessarily represent the views of RoboticsTomorrow
Comments (0)
This post does not have any comments. Be the first to leave a comment below.
Featured Product
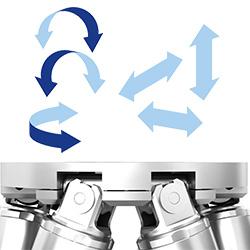