Lightweight, high-efficiency servomotors stabilize and position sensor turrets on unmanned aerial vehicles.
Contributed by | Micromo
There was a time when reconnaissance meant either multi-million dollar satellites snapping a few shots per orbit or pilots risking their necks to fly over hostile territory. Today, recon is dominated by unmanned aerial vehicles (UAVs), a much more cost effective approach that presents no risk to the operators, who are not only on the ground but frequently on the other side of the globe.
Of course, imagery is only useful if it’s crisp and clear, which requires both focusing and stabilization. That’s where Alticam Vision™ Corporation comes in. In 2001, Alticam Vision developed the first 700-gram gyro-feedback-stabilized sensor turret. This enabled a new class of lightweight UAVs weighing 15 kg and offering 24 hrs of endurance. Central to the success of these systems is a collection of compact motors from MICROMO.
CASE FACTS
Organization: Alticam Vision
Industry: UAV Unmanned Aerial Vehicles
Country: USA Challenge: Keep the turret, sensor, payload and electronics steady and aimed while countering vibration, thermal loading, wind forces and more.
Solution: Stepper motors from MICROMO
Results: A UAV that can take the heat of Afghanistan, withstand 35 Gs of force at take off and stabilize the sensor turret, to get clear images of the ground 14,000 ft below.
Ultralight UAVs are launched by catapult, suffering 35 Gs of force. (Courtesy of Insitu Inc.)
“We’re trying to squeeze as much as we can into this class of UAV, keep them small and light and affordable,” said Alticam Vision Tech President Dr. Andy von Flotow, noting that larger, more sophisticated UAVs can run around $10 million, compared to $100,000 to $200,000 for small light designs. “People have to make reservations days and weeks in advance for the big UAVs, while they can afford to distribute the smaller, more economical design widely so everyone can use them.”
Alticam Vision currently uses several classes of imagers: an Electro-Optical Daylight camera and a selection of Infrared (IR) cameras that image primarily in the mid wave and long wave IR spectral bands. The cameras produce NTSC video with fields of view on the order of 10 to 30 feet for a 1000 feet to 3000 feet altitude. Object-tracking feedback based on optical control loops allow the cameras to lock onto objects. For example, they can automatically track a truck driving along a road. Gyro-Stabilized Turrets Provide Real Time Imaging Lightweight, high-efficiency servomotors stabilize and position sensor turrets on unmanned aerial vehicles.
Dust in the Wind
An Alticam Vision turret keeps the sensor payload and electronics steady and aimed while countering vibration, thermal loading, wind forces and more. The 500-gram gyro-controlled gimbal mechanism consists of a coarse/fine design, with the outer coarse stage powered by MICROMO motors.
The sensor turret (left) on the ultralight UAVs weighs 700 g. (Courtesy of Insitu Inc.)
The turret controls both coarse axes using micro- stepping stepper motors as rate actuators, closing the loop with an absolute encoder. Why not just use a torquer, you ask? Simple, says Dr. von Flotow. “With a stepper motor, when you command a step you get one, when you command a step rate, you get that velocity. When you command a torquer, you don’t get any motion until the torque you command overcomes the friction and then it jumps, so you have to do clever friction compensation. Most people think of steppers as doing a discrete number of steps but we step these things at tens of thousands of times per second.” At such rates, friction and striation are almost irrelevant and the motion becomes nearly smooth. “It’s basically then an angular velocity actuator,” Dr. von Flotow said. The motors are teamed with dual-path spur gearboxes to produce a 200:1 reduction ratio. That yields an angular velocity of up to 90 deg/s for the axis of rotation.
In a precision pointing application like aerial reconnaissance, backlash can introduce unacceptable error. To eliminate the issue, Alticam Vision turned to MICROMO zero-backlash gearboxes. The components essentially incorporate two parallel gear trains that are wound elastically against each other. “When you use such a gearbox, it’s always a compromise between winding it too tight, generating so much friction that usable actuation torque is reduced to being useless, or winding it not quite tight enough, to where you still have a little bit of backlash,” says Dr. von Flotow. “We had to work with MICROMO to get that right. We had to develop the process together.”
The coarse stage features a large articulation, endless pan with slip rings to eliminate cable windup, and hence the need for unwind maneuvers. While the visible- wavelength imagers come equipped with motorized focus and zoom, the IR turrets also incorporate brushed DC motors from MICROMO for their focus mechanism. Some of the IR imagers also incorporate motorized zoom.
Stabilization and Control
The stabilization and control specs would be difficult to meet on the ground, but UAVs impose additional challenges. One obvious constraint is weight, but power is also an important issue. Minimizing power consumption for the turret prolongs battery life, lengthening the vehicle’s range. The cameras draw about 3 watts, and the team worked to restrict the platform requirements to the minimum, in part by using high-efficiency motors. A typical stabilizing/pointing turret draws about 4 watts, so that the entire package demands only 7 watts from the aircraft. Since the propulsion system itself demands only a few hundred watts, 7 watts is a good number for camera-system power—a 200-watts camera payload would be about as unwelcome on these small aircraft as a 5-kg payload.
Of course, even the lowest-power unit isn’t much good if it only operates in the lab. The theater of operations for UAV presents a relentlessly hostile environment. “They can get unbelievably dusty over there in Iraq or Afghanistan,” said Dr. von Flotow. “You should see some of the stuff that comes back.” It’s not just dust, either. The U.S. Navy operates a number of the lightweight UAVs, and there the issue is less dust than the salt and humidity of sea conditions. Corrosion damage is rare, though, Dr. von Flotow says. A far bigger problem is temperature.
For capture, the UAV snags a windtip on a vertical rope, for a rapid deceleration the exerts 20Gs of applied force. (Courtesy of Insitu Inc.)
“We have to watch for effects of thermal overload, first detectable in its effects upon the imagers,” he notes. “This has been an issue especially in high elevation, hot situations like Afghanistan in the heat of the summer.” The aircraft are often operated at 14,000 ft density altitude. The IR imagers require thermal stabilization, which adds weight and power demands to the system, putting more pressure on the stabilization motors to deliver motion in a small, efficient, economical package.
Of course, the challenges aren’t just restricted to the environment. The UAVs are catapulted into flight, a process that imposes 35 Gs of force on the aircraft and turrets. Even more interesting is the landing—or rather, the capture. The planes are snared in flight when they fly into a vertical rope, catching one of their wing tips. It is a method that would likely rip the wing right off a jumbo jet, but due to the advantages of scale, it simply whirls the UAV around—while subjecting it to 20 Gs of force. The turret must undergo stringent shock and vibration testing before the product is shipped, then extreme shock every mission once deployed. “We’ve had no G issues,” said Dr. von Flotow. “We’ve made them tough enough to survive.”
Indeed, the UAVs are tough right down to the motors. “We have very few, maybe even zero problems with motor failures,” says Dr. von Flotow. “The most common way for our turrets to end their lives is not being worn out. The airplanes don’t always make it home.”
For over 50 years, MICROMO (FAULHABER Group) has brought together the widest range of high quality, high performance linear and rotary motion solutions, decades of micro motion expertise based on dc motor technology and full service design, sourcing and manufacturing capability on a global basis to deliver benchmark motion solutions. Call MICROMO at 800-807-9166 and let one of our Application Engineers, design a custom motion solution for your next application.
The content & opinions in this article are the author’s and do not necessarily represent the views of RoboticsTomorrow
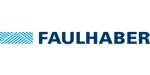
FAULHABER MICROMO
Since 1961, FAULHABER MICROMO has partnered with OEMs to deliver high precision, high performance, custom micro motion system solutions to markets such as medical, robotics and automation in North America. FAULHABER MICROMO's tradition of innovation started decades ago in Germany. The groundbreaking invention of the FAULHABER coreless winding started it all for a market that produces millions of motors today. How can the FAULHABER MICROMO team help you deliver your next innovation to market first? Learn more about MICROMO's solutions for the most demanding applications, our diverse motion products and technologies, online ordering, Engineering and R&D teams, Clean Room Assembly, Machining Center and other services at our Clearwater, FL facility at https://www.faulhaber.com.
Other Articles
Walking naturally with artificial foot
Testing drive systems virtually - Simulink library for development and digital twin.
At least 60 million strokes
More about FAULHABER MICROMO
Comments (0)
This post does not have any comments. Be the first to leave a comment below.
Featured Product
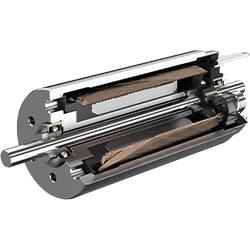