Here are three different types of rotary applications and the cable carrier system used for each.
Contributed by | Igus
Most cable carriers are capable of achieving a number of different types of rotary motion.
These movements can range from relatively simple to extremely complex and sometimes choosing the right cable carrier configuration can be a challenge.
1.1 igus® offers Twisterband for rotary applications with circular or spiral movements.
Here are three different types of rotary applications and the cable carrier system used for each:
Rotary application 1
Using standard cable carriers
In rotary applications with an abundance of installation space, a standard cable carrier (in this instance, “standard” meaning the cable carrier can only bend in one direction) can be used. This type of rotary motion has its advantages. The cable carrier system is easy to install, low-cost and capable of a moving angle up to 450 degrees.
It is important to remember that in this type of rotary application, the cable carrier will be relatively long and the length cannot be calculated. In addition, when compared to other types of installations, the cable carrier is more susceptible to wear and an increased amount of stress is placed on the mounting brackets.
1.2 An Energy Chain® cable carrier being used for a rotary application.
All igus® Energy Chain® cable carriers, Energy Tubes and Chainflex® continuous flex cables are appropriate for this kind of application.
Rotary application 2
Using cable carriers for circular and spiral movements
In rotary applications with circular or spiral movements, it is important to use a cable carrier specifically designed for this type of motion. For example, igus®’ offers two types of cable carriers that are capable of circular / spiral motions.
TwisterChain® is a rugged cable carrier that can perform circular / spiral motions up to 540 degrees and rotational speeds as fast as 13 feet per second. Thanks to its modular design, cables and hoses are easy to replace via crossbars that snap open on both sides. TwisterChain® is ideal for space-restricted applications for articulated robots, handling machines, packaging machines, glass machines, or revolving tables.
1.3 TwisterChain® being used to guide and protect cables on on a six-axis robot.
TwisterBand is a compact cable carrier that can turn through 3,000 degrees in minimal space. TwisterBand guides energy, data and media with little wear and is extremely cost effective. At high rotating speeds, the cable carrier stays close to the axis. It is ideal for rotary movements in the smallest spaces and eliminates the need for expensive rotary solutions. Twisterband can be used in a variety of applications, including medical equipment, theme park rides, radar and telescope equipment, and test, measurement, handling, lifting and installation equipment.
Rotary application 3
Using cable carriers with reverse bending radius
In applications with limited installation space, it is best to use a cable carrier with a reverse bending radius (RBR). RBR is defined by a cable carrier’s ability to travel in two different directions. Compared to both the standard and lateral systems, the length of cable carrier used in an RBR application will be the shortest. Other advantages include a moving angel up to 540 degrees, the ability to easily calculate the number of links the cable carrier will need, and increased safety due to the system’s guided parts (fixed and moving). For cable carriers with RBR, igus® recommends one cable or hose per compartment (especially in side-mounted applications) and strain relief for one side of the system.
The video below shows an example of an RBR application using an Energy Chain® cable carrier from igus®.
Almost any of igus®’ Energy Chain® cable carriers are available with RBR. We offer a number of these directly RBR from stock, but can also custom design a system for applications with special considerations.
Since each rotary application is usually different, I highly recommend taking advantage of our free consultation services.
The content & opinions in this article are the author’s and do not necessarily represent the views of RoboticsTomorrow
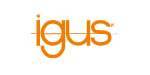
igus
The mission of igus® is to use its innovative polymer materials to develop products that provide creative solutions and exceed our customers' expectations while delivering fast, accurate service.
Other Articles
Low-Cost Robotics Elevate Industrial Inspection Processes
7 Cable Management Mistakes to Avoid
New Exoskeleton is Revolutionizing Work Processes
More about igus
Comments (0)
This post does not have any comments. Be the first to leave a comment below.
Featured Product
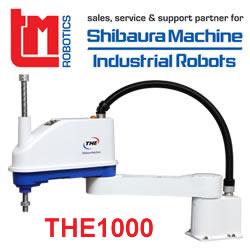