We covered a variety of recently developed ATI products including new Robotic Tool Changers, Utility Couplers, Tool Changer Modules, and other new robotic end effector products and applications.
ATI's 7th Annual Technology Training Fair
Robert Little | ATI Industrial Automation
In August you hosted ATI's 7th Annual Technology Training Fair. Tell us a bit about the event.
The event took place out of our Michigan office in Orion Township on Thursday, August 22nd. It’s a one-day event that featured four, one-hour training sessions that covered a variety of topics, all related to robotic end-effector technology. We had live robotic demonstrations and a very large group of ATI engineers and account managers on-hand to discuss applications. Our event is also located adjacent to AMT (www.appliedmfg.com), who had their own robotic and automation event during the same day.
Who attended the event?
We had a large variety of attendees from maintenance technicians to CEOs, representing a wide range of industries and markets. Some guests travelled from as far as New York, Utah, and Germany.
What do you think made the event so popular?
We offer a large variety of automation and robotics related topics that appeal to a wide range of attendees. For some of the topics covered, we offered information for free that might otherwise cost a fair amount money.
What did you have new for this year’s event?
We try to have some new topics every year. This year we had a session on Advanced Gripper and End Effector Designs from Adil Shafi at Advenovation. We also had a session that Fronius and Weber presented on alternative joining methods for metal including: aluminum welding, self-piercing rivets, and flow drill screws. Pat Davidson from the Robotic Industries Association (RIA) presented a session on the new ANSI/RIA R15.06 Robot Safety Standard and Joe Cyrek from Recognition Robotics presented a session on the Real-World Application on Vision Products.
What other topics were covered?
We covered a variety of recently developed ATI products including new Robotic Tool Changers, Utility Couplers, Tool Changer Modules, and other new robotic end effector products and applications.
What was some of the feedback from participants?
We conducted a post-event survey and received many positive comments such as: “The training sessions shared the right amount of information – both ATI products and some real-life applications.” “I felt the event was very useful and worth attending.” “Was informative and what I was looking for.” “Our time was well-spent, we picked up valuable information.”
What makes attending live events like this so much more beneficial than say online trainings or webinars?
Attendees get to engage in real-time conversation with not only ATI employees, but all the other attendees and guest presenters, to network and discuss challenges and opportunities in a very friendly, comfortable environment. Most people want that live interaction – they want to touch the products and see them in action.
What are the plans for next years event?
We’ll celebrate our 25th year in business and although we don’t have any firm plans yet, we will be sure to have something special for the event.
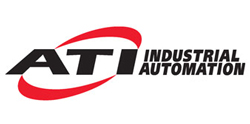
About Robert Little, Chief Executive Officer for ATI Industrial Automation
Robert Little, Chief Executive Officer for ATI Industrial Automation, co-founded the company 24 years ago. He has a master’s degree in mechanical engineering and has been awarded a variety of patents for robotic end-effector products. He has a strong belief in building the best product for the market and then improving on it. In 2012, Mr. Little helped guide the company into an employee stock ownership plan and tasked all the employees (new owners) with providing superior customer service.
The content & opinions in this article are the author’s and do not necessarily represent the views of RoboticsTomorrow
Comments (0)
This post does not have any comments. Be the first to leave a comment below.
Featured Product
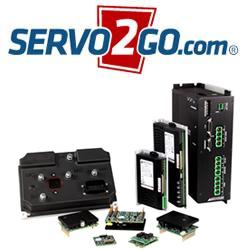
High Performance Servo Drives for localized and distributed control applications from Servo2Go.com
Engineered to drive brushless and brush servomotors in torque, velocity or position mode, Servo2Go.com offers a broad selection of servo drives in a wide range of input voltages and output power levels.