In this exciting competition, undergraduate and graduate students are invited to create a multi-disciplinary team to build a planetary rover prototype and demonstrate its capabilities to perform a series of competitive tasks in field tests at the NASA Johnson Space Centers Rock Yard in June 2013.
We were fortunate to be given the opportunity to show off some of the leading entries into the RASC-AL Exploration Robo-Ops Competition. Here are 5 of the design reports and some follup interviews with the team members:
West Virginia University - Interview
University of Nebraska-Lincoln - Interview
University of Utah - Interview
FAMU/FSU College of Engineering - Interview
Worcester Polytechnic Institute - Interview
Can you tell us a bit about your team, how you recruited, how you organized and how you are working together?
The RASC-AL RoboOps team at the University of Utah is part of the RoboUtes club. The club is an interdisciplinary student organization open to all University of Utah students, regardless of class or experience. RoboOps is the main competition that the RoboUtes attend although other competitions and secondary projects are considered each year. Members are recruited through social, educational and other outreach events hosted by either the University of Utah or by other well known institutions. Students who take interest in the club are invited to attend the scheduled club meetings where they are briefed on the tasks at hand. The students then choose to work on the tasks that most interests them. This allows for students of all disciplines and levels to work together, giving students an opportunity to learn all aspects of build.
Now at the midway point for the Robo-Ops competition how is your project coming along?
We currently have our finalized rover chassis which is being controlled through the Verizon wireless dongle using an Xbox controller. We have a single video feed that sends telemetry data wirelessly. Our sample collection system has undergone multiple physical iterations and is nearing the final build. The buggy system hardware is nearing the first full prototype. Current system testing has exceeded initial expectations and we feel comfortable with our progress.
What adjustments or changes have you made from the original plan you submitted back in December?
We have made lot of iterations to our preliminary proposal design. There have been revisions brought to the arm, chassis, software architecture and implementation strategy for both the robot and the buggy. Additional strength simulations were done at the beginning of the build season which revealed the option for windows in our chassis structures. The arm system had a complete redesign. It now uses a lead screw to actuate the elbow joint. Additional redundancy has been added to the wireless communication systems allowing mission control to remotely reset systems in case of component failure.
What were some of the challenges you have come across on the build thus far and how have you overcome them.?
One of the main goals of the group is interdisciplinary learning and cooperation. To accomplish this we try to have our members get involved with all aspects of the design, fabrication, and implementation regardless of skill level or discipline. With this strategy we ultimately end up with parts that need to be remachined, fried electronics that need to be reordered, and software that needs serious debugging. While this can be frustrating at times we feel that this is one of the best ways to learn.
How many man hours do you estimate your team has invested in the project so far?
Our team has invested over two thousand hours so far. Each person has been putting in about six hours a day, six days a week and we have a core team of four people that consistently show up and stay for the six hours. Other members of the team contribute when time allows and have contributed over two hundred hours to the project.
What are some of major tasks still yet to come over the next couple months?
We have a solid foundation for all the systems on the robot and for the next couple months we aim to build upon the foundation to add durability and software redundancy. Within the next few weeks we hope to finalize the Buggy wireless communication, vision for multiple cameras, rangefinder mount and calibration hardware , boom mechanism, sample collection box, gripper implementation, and mission control operation hardware.
What facilities and equipment do you have at your disposal for the project?
This year the College of Engineering has provided us with our own working lab which we call the RoboUtes Lair. The Lair is located right next to the Mechanical Engineering Machine shop where we have access to a waterjet, high end 3D printers, lathes, mills, grinders, sanders, and band-saws. The WiESEL lab has been kind to provide us with access to their Laser Cutter. This year the RoboUtes have acquired a hobby grade 3D printer that is located in the Lair. These machines have played a great role in manufacturing and altering our structures and prototypes.
Do you have any advice for future contenders in this type of competition?
The idea behind this competition is to bring new designs and ideas to the field of planetary exploration robotics. As such to be successful in this competition it is important that the ideas are original and are in the spirit of the competition. If a team puts up a proposal with ideas that have been seen or used before chances are they will be rejected by the committee. Secondly, it is necessary that much time is devoted for this competition. This competition cannot be achieved overnight. Its a journey of six months from design table to actual physical rover. A significant portion of this time needs to be spent in testing and iteration of your system. Lastly we feel that one of the most rewarding parts of this competition is interacting with the community. EPO activities compose a quarter of the total points, make sure to take every available opportunity and have fun.
The content & opinions in this article are the author’s and do not necessarily represent the views of RoboticsTomorrow
Comments (0)
This post does not have any comments. Be the first to leave a comment below.
Featured Product
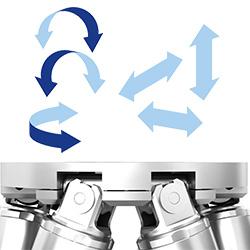