Complex position control, in combination with fast mechanical implementation of the necessary commands, represented a challenge to both developers and the integrated components.
Contributed by | MICROMO
Project studies open up future perspectives and can also inspire people. Nowhere is this truer than in the field of mechatronics, which connects three highly dynamic and growing fields offering a vast range of new developments. For this reason, GIGATRONIK Stuttgart GmbH, a mediumsized company specializing in automotive electronics and information technology, sponsored a mechatronics demonstrator as a Bachelor’s thesis. This serves for demonstration purposes at fairs and recruiting days. Complex position control, in combination with fast mechanical implementation of the necessary commands, represented a challenge to both developers and the integrated components.
Quick Reflexes Necessary
Like a human on two legs, a spherical vehicle has an unstable “stance”. It requires continuously active readjustment in order to maintain a position in the room. The procedure must be carried out very quickly, even reflexively – for the faster the reaction, the more minor necessary corrections are and the better the stability of the device. In the case presented, a vehicle equipped with electronics, electric motors and rechargeable battery balances on a ball.
The dimensions of the vehicle are approximately 30 cm x 30 cm x 15 cm, and it has a net weight of approximately 2.5 kg. Shifts in the center of gravity of the vehicle allow the ball to easily roll along on the surface. Like an artist, the vehicle is forced to balance out these rolling movements through corresponding counter-movements. To this end, a seamlessly integrated inertial sensor measures acceleration, rotation rates and the force of the earth’s magnet field on the electronic circuit board of the prototype controller “GIGABOX gate”.
A brushless motor with encoder and gearhead is the heart of the drive unit
The actual control is modeled with Simulink, transferred via a Simulink target by means of autocode generation in C-code and integrated into the controller as a realtime task. From measured data, the software computes the actual status of the overall system. The system can be seen as a three-dimensional, inverse pendulum. The pitch and roll angle are determined by a position scanner. Two PD controllers provide the necessary pulses for the stabilizing drive. These pulses are then converted by three omnidirectional drive wheels, each offset at 120° in a circle, into mechanical motion relative to the spherical surface.
Highly Dynamic and Accurate
Only highly compact motor units can be used to drive the wheels. The required dynamics narrow the options to electronically commutated motors. The optimal choice proved to be 20 mm-diameter brushless DC-servomotors with integrated encoder. Diameter-compliant gearing with a speed reduction of 14 : 1 supplements the drive package. With it, the small 20-watt drive can supply up to 0.7 Nm for short periods in order to control the position. A toothed belt reduction further boosts the torque to the wheels. The high efficiency factor on the part of the motor (70%) and gearing (80%) enables the use of smaller rechargeable batteries. The smaller dimensions here improve the vehicle’s quick reactions to position commands. The three drive units are continuously deployed independently from one another, thus converting the control commands into mechanical propulsion.
A further advantage for fast, dynamic corrections is the fact that miniature motors, especially electronically commutated variants, are generally able to withstand considerable overload for shortperiods of time. Due to the low volume, the heat radiating to the surface is comparatively high; the thermal capacity of the materials offers a further thermal buffer. The high efficiency of the unit, i.e. comparatively low power dissipation, enables such a high level of energy transfer above the rated output. In connection with the low level of moving mass, this performance virtually predestines the use of EC drives for highly dynamic functions. This is particularly the case when small installation spaces and/or very low inertial masses, e.g. on the tip of cantilever arms or robotic arms, are necessary.
Even ostensibly playful functions can contribute to the solution of problems. Small prototypes that can complete complex tasks in real time, such as here the active balancing on a ball, are costeffective research objects. Miniature drives with auxiliary modules, such as encoders, gearing and also integrated controllers, enable not only inexpensive implementations for experiments, but are also suitable for use in professional applications. The large combination variety in connection with individual case adaptation enables a customized solution for every drive task.
About MICROMO
For over 50 years, MICROMO has provided the highest quality, custom micro motion solutions for markets such as medical, aerospace, defense and robotics in North America. Decades ago in Germany, it all started with the FAULHABER coil, the landmark invention by Dr.Fritz Faulhaber. The self-supporting, ironless rotor coil design paved way for a new industry that produces millions of motors today.
A member of the FAULHABER Group, MICROMO brings together the widest range of high quality, high performance linear and rotary micro motion solutions, decades of micro motion expertise based on dc micro motor technology and complete, full service design, sourcing and manufacturing capability on a global basis to deliver benchmark motion solutions.
The content & opinions in this article are the author’s and do not necessarily represent the views of RoboticsTomorrow
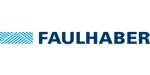
FAULHABER MICROMO
Since 1961, FAULHABER MICROMO has partnered with OEMs to deliver high precision, high performance, custom micro motion system solutions to markets such as medical, robotics and automation in North America. FAULHABER MICROMO's tradition of innovation started decades ago in Germany. The groundbreaking invention of the FAULHABER coreless winding started it all for a market that produces millions of motors today. How can the FAULHABER MICROMO team help you deliver your next innovation to market first? Learn more about MICROMO's solutions for the most demanding applications, our diverse motion products and technologies, online ordering, Engineering and R&D teams, Clean Room Assembly, Machining Center and other services at our Clearwater, FL facility at https://www.faulhaber.com.
Other Articles
Walking naturally with artificial foot
Testing drive systems virtually - Simulink library for development and digital twin.
At least 60 million strokes
More about FAULHABER MICROMO
Comments (0)
This post does not have any comments. Be the first to leave a comment below.
Featured Product
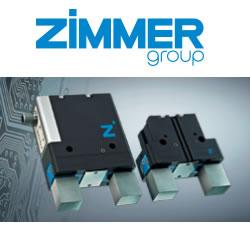