The first step in automating a process with a robot is to determine whether the tasks to be performed will require a four-axis SCARA or six-axis articulated robot, and what type and size of end effector, or end-of-arm tooling (EOAT), is needed.
Contributed by | DENSO
Manufacturers have always faced the challenge of constantly needing to find new ways to reduce the cost of their packaging processes. In today’s globally connected world, however, the game is much tougher and the stakes are much higher.
In order to meet the new challenge of sharply increased global competition, manufacturers are now being forced to cut costs more drastically than ever before. Those who do not succeed in doing so risk not only losing market share, but going out of business entirely.
Inevitably, such cost cutting means automating manual processes and increasing the level of automation of semiautomated processes. It also means re evaluating current automation solutions in light of newer, more economical technology.
Packaging has traditionally been the realm of fixed automation, often supplemented by manual labor to carry out machine tending and other intermediate process steps, mainly material handling.
For some continuous, high speed, high volume processes, fixed automation remains the best solution. Increasingly, however, manufacturers are turning to the use of industrial robots, which offer several advantages over fixed automation.
This paper will examine the benefits of using small assembly robots in upstream packaging processes, that is, those processes that occur prior to final cartoning and palletizing, both of which generally require larger size robots.
Global Competition Likely to Increase
The globalization of world markets is likely to grow even more in coming years, and at an increasingly faster pace.
As the economies of semideveloped and undeveloped countries continue to emerge, they will almost certainly result in new consumer markets, new sources of low-cost labor—and increased manufacturing competition.
As a result, the pressure on manufacturers to increase their level of automation will most likely continue to grow as well.
The Challenges of Fixed Automation
The Solution: Small Assembly Robots
4-Axis SCARA vs. 6-Axis Articulated Robots

Robot Automation Basics
Benefits of Small Assembly Robots in Packaging Operations
10 Things to Look for When Choosing a Robot
The content & opinions in this article are the author’s and do not necessarily represent the views of RoboticsTomorrow
Comments (0)
This post does not have any comments. Be the first to leave a comment below.
Featured Product
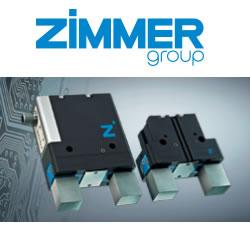