Smart Cameras Provide Additional Benefits to Auto ID Applications
Contributed by | Microscan
Today’s manufacturers need to do more with less. Tight margins, high quality expectations, and global competition have motivated manufacturers to automate their processes to improve quality and reduce costs. As an example, traceability systems that incorporate bar code readers are a standard in many industries, enabling users to document part genealogy throughout the manufacturing process and into the supply chain. Now, many manufacturers are looking to incorporate additional inspection capabilities into this process to address increasingly strict quality requirements.
System Requirements
- Read both linear and Data Matrix codes
- Ensure label presence
- Ensure proper label position/orientation
- Ensure the accuracy of the printing on the label
Solution Implementation

Results
Conclusion
The content & opinions in this article are the author’s and do not necessarily represent the views of RoboticsTomorrow
Comments (0)
This post does not have any comments. Be the first to leave a comment below.
Featured Product
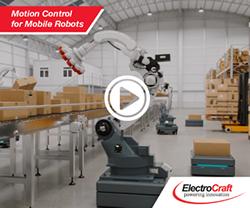