Tactics and tips for solving arc welding problems using sensors and machine vision.
Contributed by | ABB
Introduction
The purpose of this paper is to review the challenges facing manufacturers and metal fabricators attempting to automate the welding of materials with irregular, inconsistent or difficult to access joint interfaces; and established technology and recent advancements that have made robotic automation in this segment far more viable.
In principle the addition of sensors to robotic equipment will enable the automation technology to operate with remarkably human-like capabilities. When a sensor system is correctly selected, installed and trained (programmed) it will significantly extend the operational capability of the robotic arm and controller combination. In robotic welding systems the introduction of sensors provides the adaptive capability of touch and sight to address the challenges of a “moving” weld seam or component.

Historically the use of sensors with the ability to solve the problems of the moving target was not feasible for general industrial (non-automotive) type companies. The typical prohibiting factors were one or more of the following:
- The high initial investment costs
- Extended processing times
- The physical size of the sensor equipment
- The inability to achieve the desired accuracy of process
- The “stack-up” of tolerances that traditionally have precluded automated welding.
In welding applications recent and ongoing advances in sensor technology are enabling previously prohibited joint tolerances and configurations to be effectively produced with acceptable quality and weld integrity. Moreover, the technology has become performance and cost competitive for general industrial organizations, not just for the large dollar automotive and tier-one manufacturers.
There are three challenging phases of the welding process where the introduction of sensors has enabled the use of robotic automation in the welding of inconsistent joints:
Joint Edge Detection - finding the edge or start of a weld seam. A number of media have been successfully developed that effectively resolve this process demand. They generally differ in accuracy, speed of acquisition, complexity and cost.
Joint Seam Tracking - maintaining the desired weld path. In some instances the start or edge of the joint may be relatively simple to control within the tooling or fixturing. The seam itself, however, may vary due to manufacturing methodology or thermal influences of the process. Tracking of the seam by various methods can overcome this shortcoming of manufactured parts. This offers another opportunity to automate the welding of previously prohibited joints and components.
Measuring the width or profile of a joint. This helps in two ways: 1) decisions can be made to influence the robot path and speed within the joint, and 2) the process itself can be adapted to suit the local varying conditions.
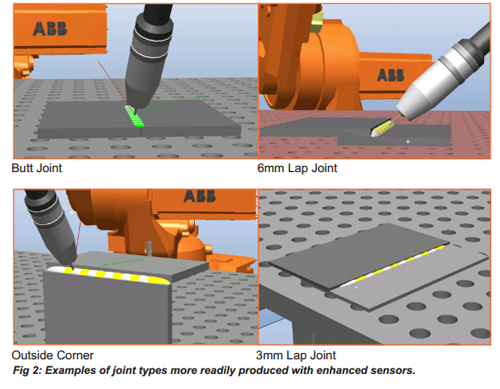
While there are a number of factors that influence the quality of a welded joint, the major sensing media capable of measuring joint width and geometry deviation have developed considerably over the last few years, greatly increasing their reliability and performance. This paper outlines how the use of emerging sensor technologies allows robotic automation to address some of the most difficult welding challenges. Specifically this paper addresses:
-
Joint Edge Detection by:
- Tactile Sensing
- A Proximity Sensor
- Joint Seam Tracking by Vision and Laser
- Joint Seam Tracking by Through-the-Arc Sensing
- Logical Considerations when Choosing a Sensor Solution
Joint Edge Detection
In determining the start of a joint or the edge of a plate, the primary sensor tools now available to the manufacturing industry are Tactile Sensing and a Proximity Sensor.
Tactile Sensing
The tactile sensing solution is well established. In principle it is a voltage applied to the welding gas nozzle, welding wire or independent probe. The prominent welding power source manufacturers all have their versions with some variations. The controller of most mainstream robotic welding systems is also able to provide this functionality. The applied voltage can differ from as low 42Vdc to whatever is legal and considered safe in the specific region of use. The monitoring or sensing for measurement can be as low as 7Vdc.
Generally the higher the output voltage the more reliable the signal, with such things as corrosion and mill scale being the main influencers.
The principle of operation for a tactile sensing system is for the voltage to short out as it makes contact on the component via either the wire, gas nozzle or an independent probe. An example of this type of sensor is SmarTac from ABB.

The short circuit is recognized by the either the robot controller or welding power source, and resulting programming decisions are then made.
An illustrative example is of a bridge deck plate being welded to a supporting ‘I’ beam. The ‘I’ beam is within its manufacturing tolerances but it varies in height in excess of the weld tolerance. So a simple touch down in the Z plane enables the height to be established. Two additional touch downs in the X and Y plane allow the robot controller to deduce the corner of the plate for the start of the weld. Tactile searches like this take between 2 to 4 seconds depending on the size of the search zone (definable) and the approach speed of search.
Proximity Sensor
The simple proximity sensor has existed for a number of years but recently the performance and reliability has become far more dependable. The sensor approach works in a similar manner as the tactile sensing system, providing an interrupt for the robot controller to make decisions. The proximity sensor, however, is non-contact and operates using an analogue inductive field. The advantage of this approach lies in the innovative skill of the robot programmer.
A well conceived, strategic route of the robot traveling over the component will provide benefits of reduced sensing time and more reliable data received.
The Proximity Sensor is attached adjacent to the welding torch, while not compromising the desired welding torch approach angles when in operation.
The robot travels over the parts and edges to be found, and any signal changes or interrupts are monitored and acted upon by the robot controller. The speed of travel and level of sensitivity are a derivative of the chosen sensor. Multiple readings from the sensor can be combined with logical instructions, providing simple X, Y and Z information, as well as angular and rotational data. The “interrupt” data can be used in number of ways, including:
- Defining a position in space to execute a weld
- Offsetting a weld seam that varies from batch to batch
- Defining a specific product to be welded automatically given a strategic search
- Calling a number of routines which may used for flexible manufacturing
- Confirming a product has been loaded correctly
With the edge or start of weld now defined by one of the previous methods the challenge now falls into two areas. Firstly it is important for the arc to remain in the correct relationship to the weld joint as it travels along the path so that weld integrity is maintained. Secondly should the weld joint change in size or geometry the process needs to be able to adapt to the local conditions to avoid a reduction in quality or worse still the potential of weld failure.

Joint Seam Tracking by Vision and Laser
The use of vision and lasers to track and modify the welding criteria on the fly are now established and proven technologies. This section provides insight into some of the considerations that need to be addressed before utilizing these processes for seam tracking. The initial and most primary consideration is that vision and laser systems are high performance options that demand a higher skill set and level of complexity than most other methods.There are three main methodologies that can facilitate seam tracking, each providing varying levels of investment, complexity and capability. They are:
- Vision solutions
- Laser scanning
- Through the arc sensors
Other solutions such as ultrasonics exist but are not yet prevalent in mainstream automation and are not considered within this document.
Historically most of the vision applications have been employed in situations where the requirements of quality were uncompromising, often with significant safety implications.

A relevant example is the railroad industry producing undercarriage bogies for passenger carriages. The build-up of these types of structures use large thick plate fabrications, forgings and castings. Such products have industry guarantee requirements of 30 years or more. The plates, castings and forgings when assembled inherently have tolerances in excess of the desired welding criteria. The introduction of a high end vision tracking solution enables these joint types to be produced with excellent results. This environment is clearly one where the higher cost threshold for such tools is much more acceptable.
Today there are more, lower cost and capable solutions available. It is important, however, to consider each system on its own merit, as not all vision/laser solutions offer the same capabilities. Without proper planning and preparation it becomes a risk that the selected process or system can either become compromised, or is incapable of performing the anticipated or desired tasks for which it was purchased.
Laser scanning technologies fall into the categories of 1D, 2D, 3D, spot, line and circle. While there are multiple uses of the various types of laser scanning options, there are some definite commonalities among them. All of the aforementioned laser types are normally combined with some form of CCD style camera to capture the images for processing with calculative algorithms.
The system is usually managed by a host PC calculating the input data and producing the necessary output for the robot to execute its task. More recent vision solutions are combining the PC and camera to make smart space saving combination

Speaking specifically, the single spot laser typically only provides a ‘Z’ value for reference. And the line method operates with either one or two laser lines. In two line systems the rotating laser identifies the offsets and the 3D calculation is achieved through triangulation.
To ensure vision/laser solutions are effectively deployed the following topics should be thoroughly considered.
- When sizing up the task, what is the smallest object or feature to be tracked/detected?
- When viewing the feature or part what level of measurement accuracy is required to meet the process criteria?
- What size of field of view is required to capture essential information when tracking?
- What is the speed of recognition and processing time required to meet output cycle requirements?
When selecting the right combination of laser and or camera there are the environmental aspects to be considered as well. Temperature, vibration, illumination and humidity all have the ability to affect the quality and reliability of the results achieved. Some cameras are best suited for static capture and others perform better for linear tracking.

The combination of process head and component geometry may also dictate what size lens and camera arrangement can be installed on the end of the robot arm. Time spent with quality 3-D simulation software is very important.
By simulating the movement of the robot and its end-of-arm-tooling, risk can be minimized by thoroughly identifying what welds can be accessed, and any potential compromises of process that may arise with certain camera/lens configurations. RobotStudio is the 3-D simulation software offered by ABB.
Over and above the physical constraints other important considerations need to be reviewed such as, does the expertise exist in your company to configure the equipment? And what level of support will be needed in the system startup and operation, and is it readily available with your chosen solution? And lastly, the calibration of the solution can be considerable and must be included in the equation of choice.
Joint Seam Tracking by Through-the-Arc Sensing
In this area we are looking to track the seam and/or volume-fill a continually changing joint configuration. For various reasons vision and laser solutions are not the preferred choice. In these cases the “thru-the-arc” approach may mean the difference between producing a repeatable, quality joint competitively through automation, or completely abandoning the automation option altogether.
Through-the-arc-tracking has evolved considerably in recent years, as the reliable, fast, and accurate tracking of a weld joint is second nature to a robot today.
A top performing through-the-arc seam tracking provides the combined benefits of economics, technical capability and physical geometry.
While the ratio of investment to capability for this type of seam tracking solution has been well established over the years, recent process advancements have continued to push out the boundaries of capability in addressing the problems of the ever-changing joint configuration. One example of such a system is ABB WeldGuide III.
The seam tracking solution requires no external apparatus to execute its tasks, providing a viable option for the numerous joint types with access challenges that precluded the use of bolt-on equipment. And, in simple economics, the capital investment of through-the-arc sensing can be as little as 10% of a comparable vision or laser solution.
The operating principle for through-the-arc sensing is to monitor the arc in order to track the seam. Through-the-arc sensing primarily uses “impedance” (not just simple volts or amps), which provides a more reliable value within the arc physics to determine accurate data.
The seam tracking operates by introducing a weave pattern, the style of which is freely programmable in time, geometry, symmetry and amplitude. A default set of weave patterns is also held in the robot controller library. The actual tracking of the joint is achieved by monitoring the impedance of the arc as the weld wire weaves from side to side. The rules of the chosen or programmed weave data will determine how the robot reacts to the changing impedance.
The changing impedance is used to modify in real time the wire feed speed (amps and fill ratio) and the robot travel speed. This combination of attributes increases greatly the variety of joints and materials that can utilize the system.

A perfect example of this seam tracking capability of a welding robot is in the manufacture of augurs. There have been a number of types of augurs that have benefited from the introduction of this sensor process.
The challenge with this type of product and joint configuration is that it is built up of complex curves in two planes. Often the materials are quite thick, difficult to bend accurately from batch to batch, and are usually tacked up in position with minimal tooling.
All of which adds the stack-up of tolerances making it nearly impossible to weld by automatic means.

This example uses a symmetrical zigzag weave with centerline tracking, causing the robot to simply stay in the middle of the joint.
Without the use of seam tracking it would require many program points along the seam for the robot to keep itself in the root of the joint. The next augur in the batch would be subtly different and all the programmed points would require modification, a lengthy and unwanted duplicative task.
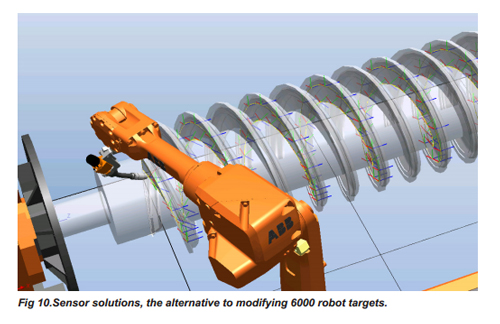
The implementation of seam tracking requires programming a few strategic points at the start and end of the weld. The use of a tactile sensor determines the start point specific to that augur. When the arc is established the robot and workpiece positioner operate in synchronous motion rotating the augur.
The tracking and weave pattern keep the arc perfectly in the root of the joint along the length of the augur for all of its rotations. In the course of operation this process has negated the influences of the stack-up of built-in component tolerances, ignored the component movement due to heat distortion, and in one simple program has created a high-integrity weld process for all the augurs of that particular configuration.
In principle, vision and laser techniques could have given the same results but the economic investment would have been significantly higher, the complexity of programming much more in depth, and the camera unit itself would have been too bulky to fit between the webs of the augur.
Another common joint which presents its own set of challenges is the lap joint. Previous generations of seam tracking traditionally required ¼ inch (6.25mm) as a minimum plate edge height that could be reliably tracked.
Today, through-thearc sensing will safely track down to an ⅛ inch (3.18mm) edge plate. This has opened up the sheet metal industry to robotic automation. A classic example is the wrapping up of sheet metal boxes like that of a cash dispenser chassis. The final fold of the box usually leaves the edge of a plate that requires welding in an inconsistent position. The principle of registering the start point by a referencing sensor is employed as before.
The use of the seam tracking is subtly different here. In this case a single sided weave is deployed.
Because there is no second feature to monitor, the impedance is only tracked on one side of the arc. The net result is the arc and robot uniformly follow the edge of the plate. The principle of this approach has been known to solve many lap joint problems.

With the vast array of alternative sensor systems available, the due diligence required to identify and select the right technology should not be underestimated. A well researched decision may make the difference between a robotic investment that meets its quality and output expectations, or in the worst case scenario, having to revert back the previous manual methodology.
When researching the appropriate sensor technologies consider:
- The materials you are working with.
- What are the attributes that are changing and by what magnitude?
- Are there cost effective steps that you can take to reduce, control or remove the deviation?
- The option of investing in a sensor solution compared to using a different joint or manufacturing methodology that will remove the condition.
- What component cost can the product absorb and still be competitive?
- Or, alternatively, what will be the savings be by reducing the rework due to introducing the sensor solution?
- What is the impact on the consumable consumption by the introduction of the sensor solution? Is it positive or negative?
- What is the impact to your business when the issue goes away by developing an effective use of a sensor solution?
With the above list reviewed and answered in a methodical and accurate way you will increase your ability to choose the right solution. If after all the above conditions are understood and you still are unsure, put it to test. Carry out trials in an industrial environment to confirm it will meet your expectations.

Summary
The overall technology advances have lowered the threshold of when sensors can be safely and effectively deployed to achieve the ultimate goal of producing components that meet the demands of the required process tolerances.
Though rigorous development and innovation the capabilities and reliability of sensor solutions have become commonplace and expected in the marketplace.
If you have products that are low in volume and inconsistent by nature, there is now a high probability that they can be effectively produced by robotic means.
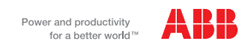
For more information please visit www.abb.com/robotics to find the contact information for the ABB office in your area.
The content & opinions in this article are the author’s and do not necessarily represent the views of RoboticsTomorrow
Comments (0)
This post does not have any comments. Be the first to leave a comment below.
Featured Product
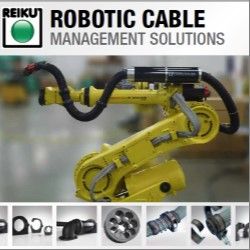
REIKU's Cable Saver™ - The Most Versatile Modular Robotic Cable Management Solution
REIKU's Cable Saver™ Solution eliminates downtime, loss of revenue, expensive cable and hose replacement costs, maintenance labor costs. It's available in three sizes 36, 52 and 70 mm.
All of the robots cables and hoses are protected when routed through the Cable Saver™ corrugated tubing.The Cable Saver™ uses a spring retraction system housed inside the Energy Tube™ to keep this service loop out of harms way in safe location at the rear of the Robot when not required. The Cable Saver™ is a COMPLETE solution for any make or model of robot. It installs quickly-on either side of the robot and has been tested to resist over 15 million repetitive cycles.
REIKU is committed to providing the most modular, effective options for ensuring your robotic components operate without downtime due to cable management.
www.CableSaver.com