While every operation brings a unique set of requirements and challenges, three sample applications that utilize barcode and machine vision technology to ensure labeling accuracy are outlined in this paper.
Contributed by | Microscan
100% Label Accuracy with End of Line Inspection Systems
Accurate labeling is essential to today’s food and beverage manufacturers, who need to cut costs, improve quality, and ensure accuracy in their packaging process in order to meet increased customer expectations, address a more competitive marketplace, and minimize the potential for product recalls. Mislabeled products pose a safety risk for consumers with allergies, and represent an enormous liability to the company in the form of costly recalls and associated lawsuits.

End of Line Barcode System Detects Incorrect Labels in Food Packaging Facility

Machine Vision Utilizes OCR to Verify Contents in High Speed Canning Line

Machine Vision System Ensures Print Legibility and Label Presence in Bottle Labeling Operation

Summary
Package Inspection Solutions from Microscan
The content & opinions in this article are the author’s and do not necessarily represent the views of RoboticsTomorrow
Comments (0)
This post does not have any comments. Be the first to leave a comment below.
Featured Product
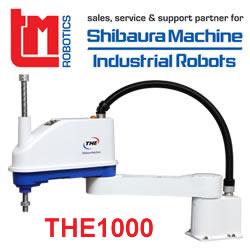