Compass Automation has rapidly become an industry-leading provider of high resolution, in-line vision inspection systems. In the fall of 2011 Compass completed the project highlighted below for Mitchel & Scott Machine Company, providing an automated vision inspection and thread checker system. Compass was able to provide Mitchel & Scott with an outstanding product in an extremely tight timeline. This system exceeded the quoted performance, providing a repeatability of 2 microns, a reproducability of 4 microns, and passing a Gage R&R with a score of 7.4%.
Case Study: Micron Resolution Vision Inspection Systems
Patrick O'Rahilly | Compass Automation
Customer Information:
Mitchel & Scott Machine Company is a manufacturer of precision machined components. Over the past 78 years, Mitchel & Scott has become a leader in the precision machined components industry, serving a variety of industries, including agriculture, transportation, construction, power generation, industrial, HVAC, hydraulic, and automotive. Mitchel & Scott currently employs over 200 people, operating out of a 200,000+ square foot facility in Indianapolis, IN.
Background:
Mitchel & Scott recently moved into the automotive industry, winning a contract to supply parts to a Tier 1 automotive supplier. This customer required 100% inspection of several critical part features, including internal thread pitch and depth, as well as 19 external geometric features.
Problem:
The complexity of the inspection, coupled with the required production rate (35 seconds per part), made it impossible to perform this inspection manually.
Manual Inspection Tooling: The inspection performed by Compass Automation's automated vision inspection and thread checker system was performed manually prior to installation. Performing this inspection manually requires multiple operators and a wide variety of tooling and gages (shown here).
Solution:
Compass provided a custom-designed, automated vision inspection and thread checker system, in-line with Mitchel & Scott's existing machining center. The machining center includes an out-feed conveyor, which delivers completed parts to the automated system. The automated system performs the following functions:
-
An in-feed nest accepts parts from the conveyor, utilizing a proximity sensor to alert the robot of part presence in the nest
-
The robot moves the part to a blow-off station, which removes excess cutting fluid from the part
-
The robot moves the part to the New Vista Thread Verification Unit for inspection; this unit tests the pitch and depth of the part's internal threads
-
The robot moves the part to the vision inspection station, where a custom-designed inspection system measures several geometric features on the part, including diameters, heights, etc. This system includes:
-
IMPERX 16 Megapixel Bobcat Camera
-
Opto-Engineering Collimated Illuminator
-
Custom-designed Hypercentric lens
-
Custom software to incorporate all requisite measurement tools
-
-
The robot moves the part to an out-feed conveyor for post-processing and packaging
Solid Model of the System: Compass fully models all custom-designed systems prior to beginning the build process. Compass will work with the customer throughout this process, utilizing customer feedback to ensure the final system meets the customer's needs. Only after completing a final design review will Compass begin to build the system.
Performance:
Ultimately, the system delivered by Compass made it possible for Mitchel & Scott to perform the 100% inspection required by their customer. The system also passed the requisite 10% Gage R&R by an extremely comfortable margin.
At each stage of the process (design, build, and install), Compass went above and beyond to not only meet, but in many instances exceed Mitchel & Scott's expectations. Specifically, Compass was able to:
-
Provide an expedited delivery timeline, delivering a finished machine in 13 weeks as opposed to the 16 week timeline that was quoted
-
Provide a higher resolution than originally quoted, providing sub-micron resolution, up from the projected 5 micron resolution
-
Incorporate 5 additional measurements after the design review and machine acceptance
-
Utilize an existing Mitchel & Scott robot, reducing the system cost by over $25,000
The Finished System: Compass completed the design, build, programming, and integration of this system in 13 weeks.
Compass Automation
Compass Automation is an Elgin, IL based company that provides customized integration services of industrial robots and automation equipment for industrial companies in North America.
Compass delivers superior Robotic Consulting, Robotic Cell Integration, End-of-Arm Tooling, Software Installation, Safety System Integration, Automation Equipment and Systems Maintenance to meet your company's unique and ever-changing needs.
The content & opinions in this article are the author’s and do not necessarily represent the views of RoboticsTomorrow
Comments (0)
This post does not have any comments. Be the first to leave a comment below.
Featured Product
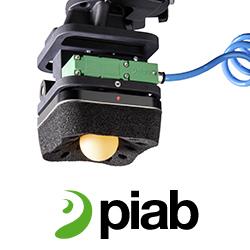