Parallel-link robot deployments will continue to see strong growth as more and more operations across all industries embrace automation as a way to cut costs and stay completive. When light payloads and very fast cycle times are required, whether it be assembly, picking, dispensing, or any number of other applications, parallel-link robots will continue to meet the challenge.
David Bruce & Raad Asmaro | FANUC Robotics America
Since the invention of the parallel-link robot back in the early 1980’s, it has evolved into an innovative and high-speed solution for a wide range of assembly, picking and material handling applications. A parallel-link robot’s actuators act on the tooling or work-piece in parallel rather then in series. With a conventional or serial link robot, each axis moves each successive axis’ actuators all the way to the tooling interface. For a six-axis robot this means that axis one moves the tooling and work-piece and all the actuators for axes two through six. With a three-axis parallel-link robot, each axis is connected directly to the tooling interface. The movement of these three axes (either one or a combination of all three) will move the tooling interface in XYZ. A fourth axis can be directly connected to the tooling interface to generate rotation. Because each axis only needs to accelerate the tooling interface, much higher acceleration rates occur, which may result in reduced cycle times compared to a serial robot. Top speeds of 10 meters per second are typical for most parallel-link robots. In addition to high speed performance, another significant advantage of a parallel-link robot is improved accuracy at the tool tip.
Parallel-link robots were initially deployed with great success in three and four-axis variations in the picking and packaging industry. A picking application is one where the output is a specific pattern of product and the input is a random or semi-random stream of that same product. Often, machine vision and conveyor tracking are employed directly with several parallel-link robots in one large picking system handling an overall system throughput of several hundred parts per minute. Packaging involves placing several products into a package such as a shipping box or other container. Often the output of a picking system will flow directly to a packaging application. Many different industries make use of picking systems, including food, medical, electronics, cosmetics, etc.
Parallel-link robots were initially deployed with great success in three and four-axis variations in the picking and packaging industry. A picking application is one where the output is a specific pattern of product and the input is a random or semi-random stream of that same product. Often, machine vision and conveyor tracking are employed directly with several parallel-link robots in one large picking system handling an overall system throughput of several hundred parts per minute. Packaging involves placing several products into a package such as a shipping box or other container. Often the output of a picking system will flow directly to a packaging application. Many different industries make use of picking systems, including food, medical, electronics, cosmetics, etc.


The M-1iA and M-3iA
FANUC Robotics offers two variations of parallel-link “Genkotsu” robots. The FANUC M-1iA is a lightweight and compact four or six-axis, parallel-link robot designed for small part handling, high-speed picking, packing, and assembly applications. Its very small foot print and envelope allow it to be installed next to a manual operation with minimal engineering. The M-3iA robot is a larger version of the M-1iA. Available in a four- or six-axis model, the M-3iA offers the same unique parallel-link structure, and accommodates payloads up to 6kg. In addition, it has the largest work envelope of any robot in its class (1350mm x 500mm). FANUC Robotics refers to its series of parallel-link robots as “Genkotsu” or fists because they provide the accuracy and flexibility of a human hand.
The M-3iA is now working in a variety of industries from an automotive engine facility to scoring of un-baked bread. Compared with most parallel-link robots that are limited to either three or four-axes, the FANUC M-1iA and M-3iA are unique. The six-axis variant combined with a three-axis wrist allows for the completion of tasks which involve manipulating parts and/or tooling at compound angles. By combining a three-axis wrist with the speed and precision of a parallel-link robot, and the integrated intelligence offered by all FANUC robots, FANUC Robotics is rapidly making possible the automation of many tasks which are now either manual or done by expensive hard automation.
Intelligence is more than just a buzz word in the robotic industry, it is an ever-increasing reality. Both force control and machine vision are becoming more and more prevalent as part of industrial robot systems, especially with assembly operations. In an ideal world, parts line up and fit perfectly; however, in the real world work pieces require a wiggle or visual adjustment. Machine vision and force control are increasingly able to handle these realities, and when combined with a parallel-link style robot, the cycle time of each operation falls dramatically, which reduces the number robots required and the return on investment timeline! With picking applications, machine vision is employed in conjunction with conveyor tracking to accurately track a random product on a moving conveyor belt at speeds as high 1400 mm/sec (275 ft/min). The machine vision camera will continually snap and locate product at some point upstream of the parallel-link robots. When a product is identified by the camera, its location is combined with the current position of the conveyor belt. As the product enters a robot work area the robot is able to accurately move to the product and either pick it or work on it while matching the current conveyor speed. Parallel-link robots are the preferred style for this type of application since the amount of time the robot deals with each product needs to be as short as possible in order to maintain the usually very high system throughput.
While the payload of parallel-link robots is considerably less than that of serial robots (6kg vs. >200kg) their use of intelligence is still as strong. Remote force sensing is now used to accomplish difficult assembly applications quickly using six axis parallel-link robots. By remote mounting the force sensor, small six-axis parallel-link robots are able to make use of this game changing technology. Vision cameras can be mounted directly to a parallel-link robot’s tooling, or fixed-mounted in the robot’s work envelope.
Machine vision is increasingly used for inspection either before a part is put into an assembly or after the assembly process is completed, and Parallel-link robots can make this process quicker and more cost effective. How? By simply adding a single camera to several different inspection points or to an existing assembly to catch problems before they happen, or eliminate bad assemblies from the supply chain before they enter it .
Like all robots, parallel-link robot deployments will continue to see strong growth as more and more operations across all industries embrace automation as a way to cut costs and stay completive. When light payloads and very fast cycle times are required, whether it be assembly, picking, dispensing, or any number of other applications, parallel-link robots will continue to meet the challenge.
The M-3iA is now working in a variety of industries from an automotive engine facility to scoring of un-baked bread. Compared with most parallel-link robots that are limited to either three or four-axes, the FANUC M-1iA and M-3iA are unique. The six-axis variant combined with a three-axis wrist allows for the completion of tasks which involve manipulating parts and/or tooling at compound angles. By combining a three-axis wrist with the speed and precision of a parallel-link robot, and the integrated intelligence offered by all FANUC robots, FANUC Robotics is rapidly making possible the automation of many tasks which are now either manual or done by expensive hard automation.
Intelligence is more than just a buzz word in the robotic industry, it is an ever-increasing reality. Both force control and machine vision are becoming more and more prevalent as part of industrial robot systems, especially with assembly operations. In an ideal world, parts line up and fit perfectly; however, in the real world work pieces require a wiggle or visual adjustment. Machine vision and force control are increasingly able to handle these realities, and when combined with a parallel-link style robot, the cycle time of each operation falls dramatically, which reduces the number robots required and the return on investment timeline! With picking applications, machine vision is employed in conjunction with conveyor tracking to accurately track a random product on a moving conveyor belt at speeds as high 1400 mm/sec (275 ft/min). The machine vision camera will continually snap and locate product at some point upstream of the parallel-link robots. When a product is identified by the camera, its location is combined with the current position of the conveyor belt. As the product enters a robot work area the robot is able to accurately move to the product and either pick it or work on it while matching the current conveyor speed. Parallel-link robots are the preferred style for this type of application since the amount of time the robot deals with each product needs to be as short as possible in order to maintain the usually very high system throughput.
While the payload of parallel-link robots is considerably less than that of serial robots (6kg vs. >200kg) their use of intelligence is still as strong. Remote force sensing is now used to accomplish difficult assembly applications quickly using six axis parallel-link robots. By remote mounting the force sensor, small six-axis parallel-link robots are able to make use of this game changing technology. Vision cameras can be mounted directly to a parallel-link robot’s tooling, or fixed-mounted in the robot’s work envelope.
Machine vision is increasingly used for inspection either before a part is put into an assembly or after the assembly process is completed, and Parallel-link robots can make this process quicker and more cost effective. How? By simply adding a single camera to several different inspection points or to an existing assembly to catch problems before they happen, or eliminate bad assemblies from the supply chain before they enter it .
About Author
FANUC Robotics America, Inc., is the leading supplier of robotic automation in the Americas, Over 220,000 FANUC robots are installed worldwide, and more than 200 robot variations work in a wide range of applications.
The content & opinions in this article are the author’s and do not necessarily represent the views of RoboticsTomorrow
Comments (0)
This post does not have any comments. Be the first to leave a comment below.
Featured Product
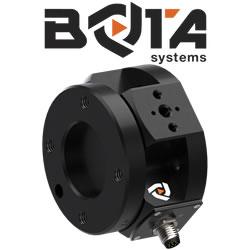
Bota Systems - The SensONE 6-axis force torque sensor for robots
Our Bota Systems force torque sensors, like the SensONE, are designed for collaborative and industrial robots. It enables human machine interaction, provides force, vision and inertia data and offers "plug and work" foll all platforms. The compact design is dustproof and water-resistant. The ISO 9409-1-50-4-M6 mounting flange makes integrating the SensONE sensor with robots extremely easy.
No adapter is needed, only fasteners! The SensONE sensor is a one of its kind product and the best solution for force feedback applications and collaborative robots at its price. The SensONE is available in two communication options and includes software integration with TwinCAT, ROS, LabVIEW and MATLAB®.